Design of electronic board test benches
The test engineering department provides a complete test strategy, from the testing of electronic equipment in production, in the laboratory and on customer sites.
A dedicated team at TRONICO designs, implements, optimises and maintains test facilities for complex systems with a focus on electronics. These test facilities have levels of automation adapted to requirements and are intended for testing mass-produced products on their production lines, for validation tests in the laboratory, and for remote or mobile functional tests on the customer’s site, in support of the reliability, technologies and innovation of their products.
TRONICO's global offer
Description
Services
Design: throughout their lifecycle, electronic equipment needs to be tested. A dedicated team in the design office develops these test systems.
Integration: each test device is manufactured at least once, often several times. Production technicians carry out these integration, duplication, fine-tuning and validation activities.
Changes: it may be necessary to make changes to the test bench. This can happen, for example, when the product under test evolves or when production rates change. The design office takes charge of these changes (adding functions, improving performance, etc.).
Maintenance: like all installations and equipment, test benches require maintenance. The TRONICO quality team and laboratory jointly carry out all these operations (calibration, return to operational condition, etc.).
Applications
TRONICO is able to design three types of test benches:
Production test facilities for electronic equipment manufactured in small or large series: these testers are designed to reduce operator risks, cut manufacturing costs, increase production capacity and be scalable.
Laboratory test benches for qualification: their purpose is to validate the designs of predominantly electronic products and to obtain their certification. They are designed on a modular basis to meet the specific technical requirements of each test, while keeping costs under control.
Cases dedicated to on-site testing: these enable tests to be carried out in buildings, outdoors or on board vehicles (automotive, aeronautical, marine, etc.). These test cases are designed to be mobile and to withstand the most extreme conditions of travel and use.
Level of automation
All our test equipment is designed with different levels of automation:
Manual test systems: affordable because of their low cost, they require the continuous intervention of an operator, making them an attractive solution for smaller production runs or rapid, low-tech tests.
Semi-automatic test benches: frequently used, these testers require the occasional intervention of operators and offer the best compromise between cost, performance and lead times. They are used for intermediate production runs and can perform the simplest to the most complex operations.
Automatic test benches: requiring a major design effort, they enable tests to be fully automated. They are ideal for very large production runs or for long, complex tests.
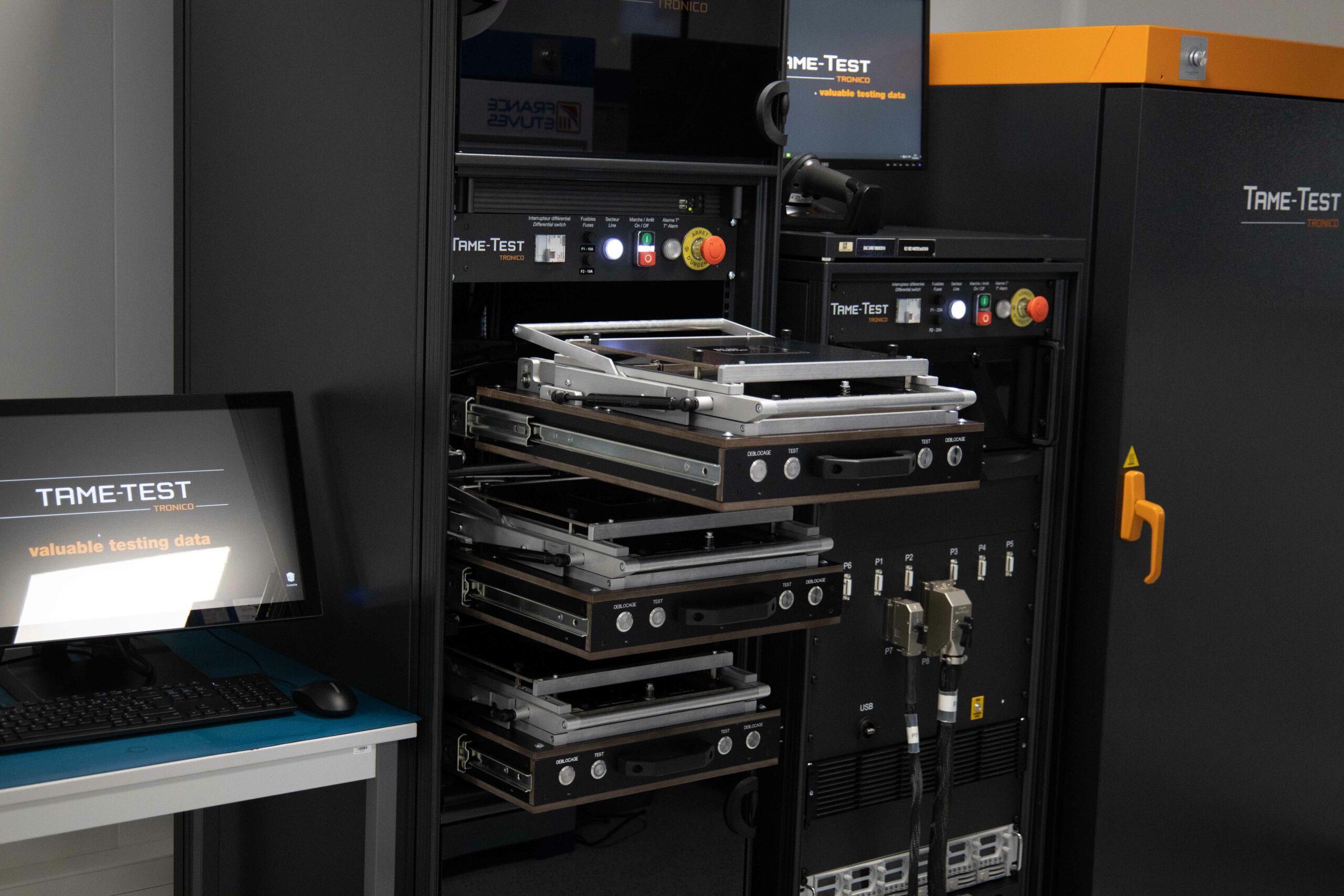
Benefits
The strengths of an EMS
*EMS = Electronic Manufacturing Services
The professions :
The team dedicated to testability is located at the heart of TRONICO’s premises. On a daily basis, it benefits from all the strengths of the company’s departments. For example
Test facility components and equipment are included in TRONICO’s overall annual purchasing budget during negotiations with suppliers. The equipment purchased for the test facilities then benefits from significant cost reductions.
Like all design projects, the design of test and trial facilities is monitored by the quality department. Compliance with processes, validation of deliverables and milestones are therefore subject to internal and customer arbitration to provide our customers with project visibility and the fulfilment of commitments.
Historically a manufacturer of electronic boards, TRONICO has all the skills and tools to design its test facilities in such a way as to optimise production. With expertise ranging from components through electronic board manufacture to the integration of complete equipment, Tronico has complete control of the test chain applied to the production flow. This all-encompassing vision of testability enables us to provide original, higher-performance, more reliable solutions at lower cost.
Finally, the project team organisation means that the development of testers can be addressed by business sector. In this way, documentation is adapted to market needs and applicable standards.
Project management:
The design engineers support the test resources team with their multidisciplinary expertise in the development of electronic equipment. This provides them with both a tried and tested design method and an understanding of the products under test:
The method used to develop the test facilities is strongly inspired by that applied to the design of electronic equipment. The team applies a tried and tested process that is efficient and enables the development of complex, multi-disciplinary solutions. As a deliverable of this process, the technical definition files enable safe, efficient, rapid and economical duplication of test benches.
This experience of designing products for different sectors of activity enables the team to integrate the different technical sensitivities and standards requirements into the development of test benches in these fields.
Divided into different areas (mechanics, electronics, software, multi-physics, etc.), the technical department is able to provide multi-disciplinary and innovative technical expertise for the design of test facilities.
Analogue, digital and power electronics are Tronico’s core business. This specialisation means that we have complete control over the test equipment designed and the products tested, whatever their field of application.
Finally, access to embedded and high-level software development skills and tools enables the test bench design team to develop their own software, while providing cost-effective and original solutions compared with those on the market.
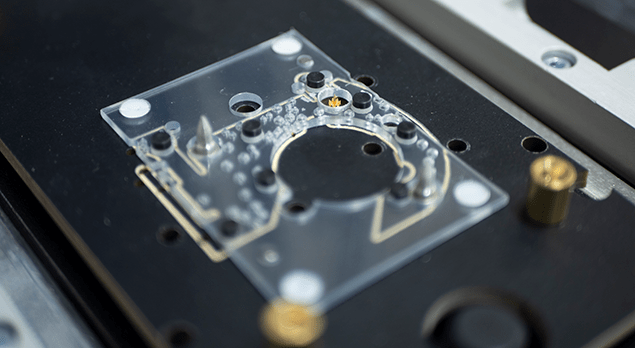
Experience in test and trial facilities
A dedicated team:
The team dedicated to the design of test and trial equipment has been part of the Technical Department since its creation, before becoming a separate entity under the Tame-Test brand.
It benefits from over 15 years’ experience, which has enabled it to capitalise on and develop tried and tested standard solutions that can be reused from one design to the next.
The test benches benefit from a modular architecture that enables solutions to be adapted to customers’ needs while reducing design times. This architecture has been tried and tested on a number of projects, and the use of feedback guarantees that the level of control and quality will always be improved.
The proximity of electronics specialists with expertise in electrical and electronic measurements means that complex, high-performance measurement chains and instrumentation can be put in place. The team benefits from strong technical support in EMC and signal processing. This support ensures the best possible measurement and test performance.
The proximity of mechanical designers means that studies can be carried out.
Proven solutions
The development of numerous industrial test benches has enabled TRONICO to build up a library of solutions that are reusable, standard, customisable, tried and tested and scalable. Here are a few examples:
- Standardisation of control and measurement cards compatible with the rack format.
- A tracer that records in detail all the actions and events that take place on the test bench.
- Centralised, secure database for storing test results.
- Test HMI to guide the operator through the various stages of the test process.
- Statistical module for processing the database using statistical or probability calculations for prevention and prediction.
- Debug interface for debugging electronic equipment by development teams or after-sales service.
- Remote maintenance, enabling you to intervene directly on the customer’s site without having to travel.