Manual and SMD assembly of electronic boards
The electronic boards entrusted to TRONICO undergo various processes: screen printing, SPI (Solder Paste Inspection), placement, reflow and 3D AOI for SMT, preparation, preparation before standard or selective wave, X-ray inspection, board cleaning (manual or machine) and, finally, manual soldering, tropicalisation varnish, potting and mechanical assembly.
Description
TRONICO is a traditional subcontractor specialising in the manufacture and assembly of printed circuit boards, with an active training unit (more than 5,000 hours per year). TRONICO assembles more than 85,000 boards per year for 15,000 different part numbers, indicating the diversity of designs addressed by our teams. The finish of our PCBAs is IPCA610 class 3 only, i.e. high-performance, reliable electronic products that function in a critical environment (vibration, salt, dust, extreme temperatures, humidity) for aerospace, medical, military and energy applications.
TRONICO's global offer
Features of TRONICO
From small to medium production runs
TRONICO is the EMS for made-to-measure boards, from small to medium production runs and with a high degree of flexibility for the boards to be industrialised!
TRONICO manufactures boards from double-sided to 24 layers on all types of substrates (rigid, flex and flex-rigid, epoxy, ceramic, polyimide or Teflon) and finishes (gold, tin, lead, silver, copper).
Different brazing alloys are used depending on the final technical characteristics of the brazed joint required: mechanical strength, electrical and thermal conductivity. There are alloys with and without lead (Rohs).
One of the challenges is the robustification, densification and miniaturisation of components.
Particular attention is paid to the incoming inspection and storage of components, and their drying or vacuuming (drypacks or dry cabinets).
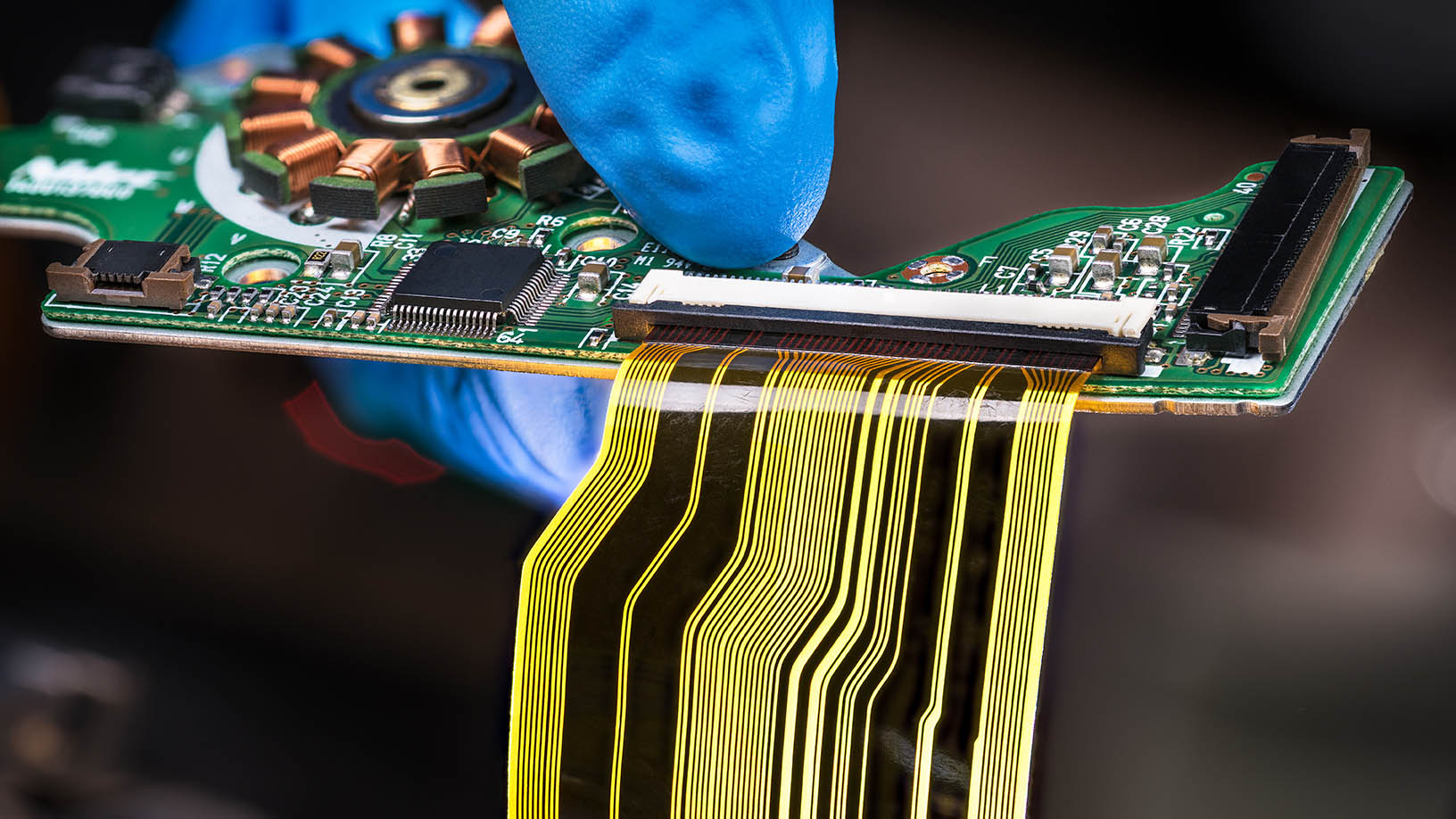
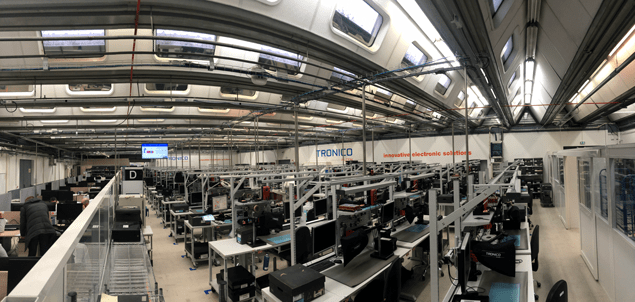
Recent machinery
TRONICO’s machinery is recent, benefiting from regular investment to ensure the quality of our products and the work of our employees.
SCREEN PRINTING AND CMS WORKSHOPS
SILK SCREEN PRINTING
DEK Horizon 3I machine
- Screen printing of cards up to 610mm x 508mm (6kgs max)
- Screen printing up to 01005, µBGA at 0.4mm pitch
- Max board height 43mm
- Held in place by Gridlok support or magnetic pins
- Stainless steel or nickel laser machined screens / stepped stencils
- 2D inspection
- Instinctiv interface
DEK Horizon 2i machine
- Screen printing of cards up to 610mm x 508mm (6kgs max)
- Maximum height under card 43mm
- Held in place by Gridlok support or magnetic pins
- Stainless steel or nickel laser machined screens / stepped stencils
- 2D inspection
- Instinctiv interface
EKRA Serio 4000
- Screen printing of boards up to 610mm x 510mm (6kgs max)
- Screen printing up to 01005, µBGA at 0.4mm pitch
- Alignment repeatability ± 12.5 μm @ 6 Sigma
- Held in place by Variogrid support or magnetic pins
- Dimensions: 1180 x 1840 x 1450 mm
- Stainless steel or nickel laser-machined screens / stepped stencils
SPI
PRIMO L
- Solder cream dispensing control machine
- Placement of boards up to 609mm x 533mm
- Type of defects checked: excess, missing, missing paste, bridge, etc.
- 2D and 3D shape
CMS
2 EUROPLACER IINEO ROBOTS
- SMD placement on boards up to 700mm x 460mm
- 12-nozzle placement head
- Loader capacity: 231 positions x 8mm + Jedec storage positions: 10 internal trays or 30 external trays
- Max speed: 30000cph (IPC placement speed: 24200cph)
- Placement of 0201, µBGA components with 0.4mm pitch, connectors up to 50mm
- Fixed camera (analysis of components >50mm)
ATOM ROBOT
- 2 pipette heads
PARAGON 125N BTU OVEN
- 10 top/bottom heating zones for a heating length of 126 inches (3.2m)
- Maximum temperature: 350°C
- Forced cooling over a length of 1.2m (external cooling unit) can be parameterised
- Conveying of boards up to 610mm wide
- Theoretical nitrogen consumption (25-28m3/h <100ppm)
- Furnace compatible with RoHS process
- Weekly monitoring of equipment by measuring capability (Cpk > 1.33) and periodic full requalification (every 3 years)
SOLTEC MyReflow 1020 furnace
- 10 heating zones (top / bottom) for a heating length of 3.5m
- 2 cooling zones (0.7m)
- Conveys boards up to 610mm wide
- Max. temperature 350°C
- Atmosphere: air or nitrogen (≤750ppm)
- RoHS compliant
IBL VAC 645 vapour phase
- Maximum board size: 635mm x 444mm (fixed board)
- Maximum board weight: 5kg
- Maximum component temperature: 235°C (Galden235)
- PLC: up to 50 programs
- Vacuum module with external pump
MANUAL WORKSHOPS
There are 80 manual workstations equipped with :
- Computerised access to all manufacturing instructions (paperless since 2008)
- Several workstations equipped with hot plates
- Latest-generation soldering irons
- All our workstations are equipped with LEICA binoculars
WAVE WORKSHOPS
The main elements available in the wave workshops are :
- Delta Wave Max
- Delta Wave
- Selective wave
- Stripping/tinning
POTTING, VARNISHING AND UNDERFILL
Potting (resin) and varnishing protect the components and the printed circuit from their environment (humidity, salt, dust, vibrations, etc.).
- Several varnish application processes are used: brush, dip or spray varnishing. Depending on the product’s operating environment, several types of varnish are available, under controlled temperature and humidity conditions.
- Potting by casting resin adapted to the product
- Underfill: application using 3-axis robots