TRONICO: electronics supplier to the aerospace and aviation industries
Driven by the need to optimise aircraft performance, reduce operating and maintenance costs, increase reliability and cut emissions, the aerospace industry is turning to new electronic solutions.
TRONICO's expertise in the aerospace marke
TRONICO is a major player in the subcontracting of electronic systems for major customers in the aeronautics, defence & security and space industries.
In addition to its core business of EMS (Electronic Manufacturing Services), TRONICO is positioned as an EDS (Electronic Design Services) in the development of complex systems with a predominance of electronics and offers its expertise in :
- Industrialisation
- Best-cost manufacturing
- Maintenance in Operational Conditions (MCO)
- Design and maintenance of test resources
Industrialisation
Industrialisation looks for and analyses reliable and sustainable solutions to optimise the manufacture of electronic assemblies. TRONICO’s industrialisation service facilitates and supports the transition from prototypes to series production. This industrialisation phase starts at the very beginning of the project in order to optimise production costs in the short, medium and long term.
The industrialisation cycle includes :
- FMEA (Failure Modes, Effects and Criticality Analysis) purchasing and supply: TRONICO manages risks and obsolescence thanks to its knowledge of the market.
- Process FMEA: TRONICO assesses and manages production risks
- DfX (Design for X)
- DfM (Design for Manufacturing): analysis of board manufacturability and integration
- DfT (Design for Test): definition and optimisation of the test strategy
- DfA (Design for Assembly)
These services are provided by the MPI (Méthodes Procédés et Industrialisation) department, which acts as a link between the designer and the manufacturing operator.
The cost and quality constraints demanded by the aerospace industry require the use of methods derived from the automotive industry, such as APQP (Advanced Product Quality Planning), encouraged by GIFAS (Groupement des Industries Françaises Aéronautiques et Spatiales). The use of these methods makes it possible to integrate feedback from past developments and ensure perfect control of processes through measurement loops.
Best-cost manufacturing
In 2003, TRONICO set up an electronics plant in Tangier, Morocco.
With 500 employees, NADCAP and EN9100 certifications and an IPC A610 class 3 quality level, this factory works mainly for the civil aeronautics industry and remains the leading aeronautics electronics factory on the African continent.
Depending on requirements and the nature of the product, TRONICO can offer production at its French and/or Moroccan sites.
The Saint-Philbert-de-Bouaine and Tangier sites are identical in terms of equipment, processes and certifications.
At the heart of the business continuity plan, resources and processes are fully compatible between the two sites.
Maintaining Operational Conditions (MOC)
The lifespan of aircraft can exceed 30 years, unlike the marketing lifespan of electronic components, which is becoming shorter all the time. Faced with obsolescence problems (components, processes, manufacturing files, etc.), TRONICO offers MCO (Maintenance in Operational Conditions) solutions:
- Detection of counterfeit electronic components
- Obsolescence monitoring
- Re-design, reverse engineering, Form Fit Function re-engineering
- Secure storage of components, boards or assemblies
- Repair, multi-unit remanufacturing
Some activities are carried out in our component engineering laboratory (Tame-Component).
Design and maintenance of test facilities
The compliance of aeronautical electronic equipment depends in part on the tests it undergoes.
By combining the various production tests with a final functional test, TRONICO proposes an optimal test strategy for each electronic product. TRONICO designs, integrates and commissions automatic test equipment for this final phase of the production cycle.
On the basis of a test specification from its own design office or that of its customers, TRONICO will define an architecture, choose the test equipment, define an ergonomic HMI (Human Machine Interface), wire the equipment up to the interface of the system to be tested using connectors or bed of nails and provide operator training.
Bearing in mind the economic constraints of the project, the modular architecture of the TRONICO test benches means that several boards or assemblies can be tested on the same tool. What’s more, the automation of test sequences right through to the issuing of the Test Report simplifies and rationalises the daily use of the test bench by the operator.
TRONICO certifications for the aerospace marke
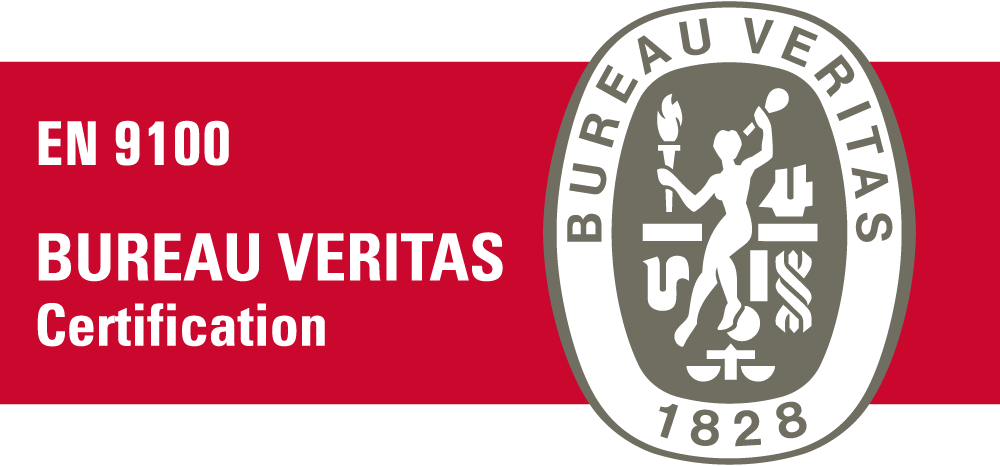
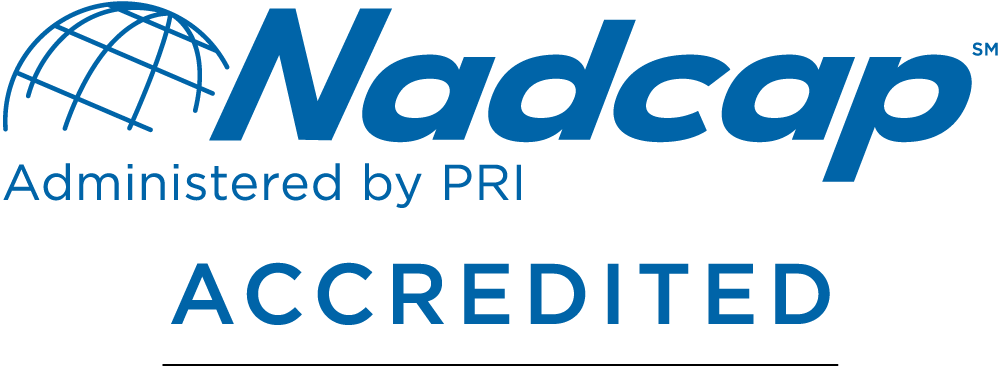
EN 9100
EN 9100 is a European standard that incorporates the principles of ISO 9001 and applies to the entire aerospace and defence supply chain.
EN 9100 is the equivalent of AS9100 (America) and JISQ 9100 (Asia).
It attests to the reliability and quality of TRONICO’s services in the design and manufacture of embedded products.
Nadcap
TRONICO is Nadcap Electronics certified, a certification of the electronic board manufacturing process developed by players in the aerospace and defence market. The aim is twofold: to improve quality and reduce costs.
The 2 production sites (Saint-Philbert-de-Bouaine in France and Tangiers in Morocco) are Nadcap certified.
The Tangiers site is the first Nadcap Electronics certified site on the African continent.
TRONICO customers in all sectors benefit from the same manufacturing processes.