The manufacture of electronic boards, TRONICO’s core business
Founded in 1973, TRONICO specialises in the design, industrialisation and manufacture of complex electronic products for third parties throughout their life cycle. In addition to its core business of EMS (Electronic Manufacturing Services), TRONICO acts as an ODM (Original Design Manufacturer) in the development of complex systems for high-reliability markets.
Our main markets are
- Aerospace
- Defence
- Energy
- Medical
- Space
Description
TRONICO specialises in high mix, low volume (small and medium-sized, highly diversified production runs), from prototyping to maintaining your product in operational condition. Two twin production units based in Saint-Philbert-de-Bouaine (Vendée – France) and Tangiers (Free Zone – Morocco) benefit from the same industrial and quality standards in the service of “zero defects”. TRONICO is France’s leading EMS in the aerospace industry, with a brand image as a first-rate partner. It benefits from 50 years’ experience, serving its demanding customers in other markets.
TRONICO's global offer
Benefits
Industrial capacity
Assembly
TRONICO has 2 electronics design and production sites, each covering 6,000 square metres. They house SMD assembly lines (surface-mounted components) and manual workshops for wiring and integration:
- 6 SMD lines on its 2 production sites to meet the requirements of our customers
(chip 01005in , board size 500*700mm) - Forced convection and vapour phase reflow processes to meet the most stringent requirements
- SPI inspection (solder paste deposition control) and latest-generation 3D AOI to improve quality
Wave soldering
- 2 selective waves
- 3 laminar waves (Leaded Alloy + RoHs)
Cabling, integration and wiring:
- Manual cabling, rewiring, mechanical assembly
- Production of cables, harnesses and strands
- Integration and testing of finished products
Various processes
Processes for protecting electronic products are used to increase the resistance of products (robustification) to severe environmental constraints:
- Coating
- Encapsulation (potting),
- Component underfill
TRONICO has the latest technological resources to meet the challenges of densification and miniaturisation: TRONICO is able to offer its customers the manufacture of boards with 01005in chip components, BGA in 0.3 pitch in compliance with IPC A610 class 3 standards.
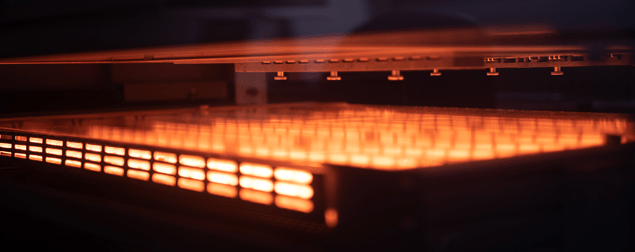
A comprehensive testing strategy
In production, appropriate tests are carried out to guarantee the best coverage or functional rate for your products:
- Structural tests: Insitu test, mobile probe test, 11,000pts insulation continuity test, etc.
- VRT (rapid temperature variation)
- Functional testing for products designed for extreme environments (vibration, dynamic burn-in, etc.)
Seasoned logistics
Supply chain management at TRONICO has a single objective: customer satisfaction. From the expression of a need (customer forecast, one of the customer departments or an order) to the delivery and invoicing of a product or service, the supply-chain department ensures that operations run smoothly throughout the product production cycle, while respecting and optimising lead times, quality and cost. Several departments are involved: industry, purchasing and operations.
TRONICO is a pioneer in the implementation of MRP II (manufacturing resource planning), enabling it to meet its contractual commitments in terms of punctuality (OTD), quality (OQD) and services (spares, repairs). Thanks to this process, TRONICO anticipates production planning: strategic plan, industrial and commercial plan (PIC), master production programme (PDP) and operational implementation. In the event of a crisis (e.g. health crisis or shortage of components), TRONICO uses all its agility to continue to produce in line with its customers’ expectations:
- direct shipment: TRONICO relies on two flows, Direct to TRONICO and Direct to CUSTOMER
- milkrun: Milkrun-Kanban flows have also been set up to meet specific customer requirements.
Resources
Human Capital
Human Capital is the foundation of TRONICO’s operational excellence:
- A highly qualified workforce dedicated to each customer
- An advanced in-house training school: between 4,000 and 5,000 hours per year, over sessions lasting 6 to 8 weeks before integration into the workshop
- Quick Response Quality Control (QRQC) teams to resolve problems in an agile and responsive mode: these are daily production rituals to ensure that production problems are reported quickly.
The Lean approach within the Operations Department:
Our teams at our 2 production sites are Blue, Yellow, Green and Black Belt certified. As part of a continuous improvement and efficiency drive, TRONICO’s teams are heavily involved in reducing waste, improving productivity and improving working conditions:
- 5 S method
- Kaizen projects
- SMED projects
- Kanban logistics
Technology watch:
Through its teams, TRONICO is anticipating tomorrow’s production developments in complex environments by getting involved in the Pleiade collaborative project:
PLEIADE (PLateforme Européenne d’Intégration d’Assemblage et de Développement Electronique – European Platform for Electronic Assembly Integration and Development) brings together players in electronics manufacturing around industrial cooperation projects led by the We Network technical centre, with the aim of improving control of electronic assembly processes in France and boosting the competitiveness of this industry, which is also widely represented in the Pays-de-la-Loire region.
Following on from the PLEIADE1 and 2 projects, the PLEIADE3 project involves pooling the efforts of the partners to develop a common methodology for characterising and assessing new-generation soldering creams used in the manufacturing process for high-integration density boards with fast high-frequency signals.
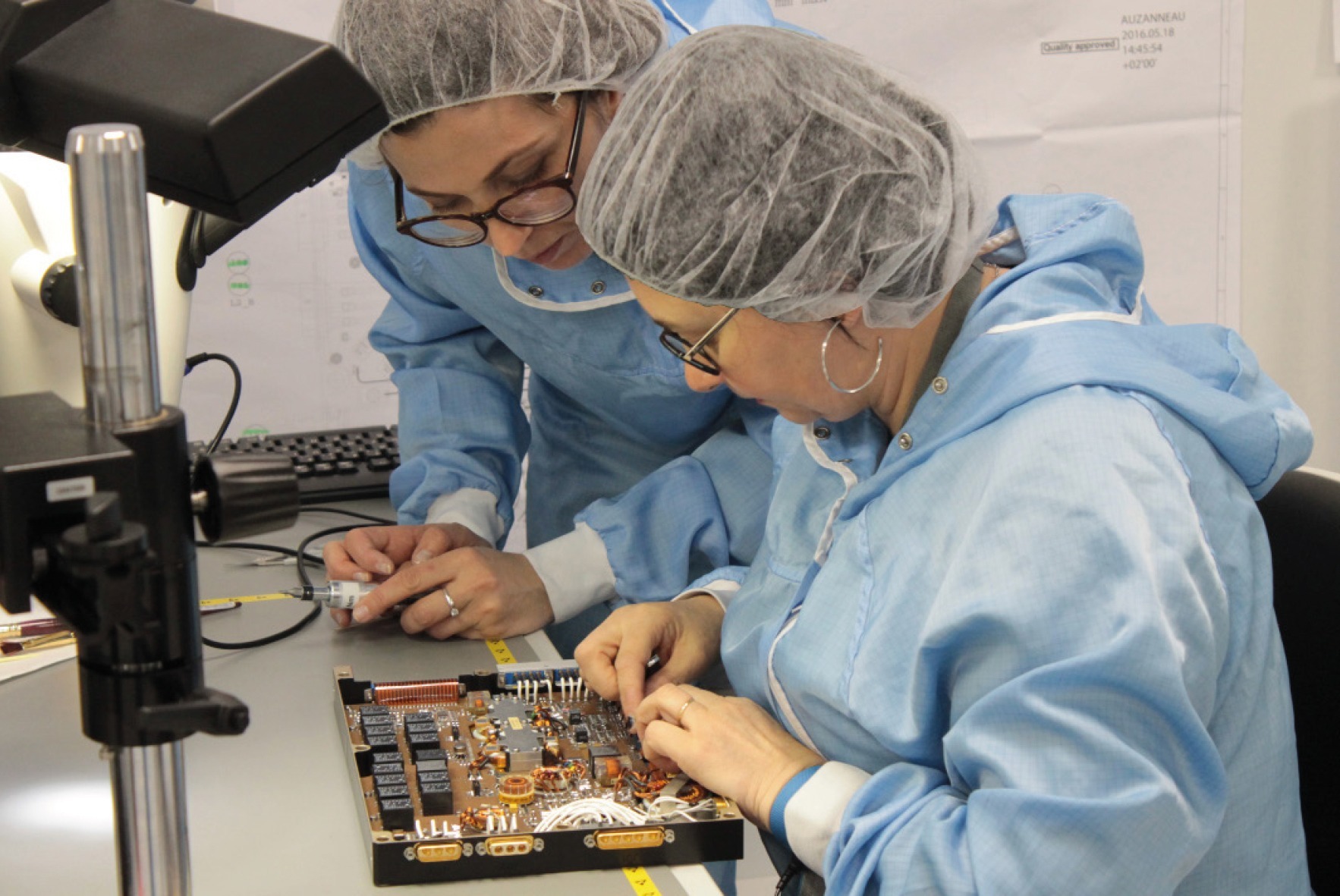
Equipment
The equipment used in production at TRONICO includes :
- testing facilities
- 3 ISO7 clean rooms for the medical, space and microelectronics industries:
These spaces are ISO 7. This cleanroom volume enables the production of products that are particularly sensitive to particle contamination. The main activities carried out in a cleanroom atmosphere include
– Class IIB – III implantable medical devices: TRONICO manufactures medical equipment for implantation in patients. The electronic boards are produced, tested and moulded into the final equipment.
– Wiring of space boards: the teams and the space clean room are accredited by CNES and ESA under a PID (Process Identification Document – Electronic Boards Soldering). Subcontracting of space electronic boards”. This room is used to carry out all manual and mechanical soldering operations on boards, de-soldering and tinning, board inspection, coating and varnishing.
– Microelectronics activity: TRONICO can carry out wire bonding on bare chips with wires up to 25µm in diameter using different types of alloys and materials. Chip transfer and encapsulation can also be carried out in-house. Pull test” and “shear test” validity tests can also be carried out in a clean room and are validated by Cofrac.